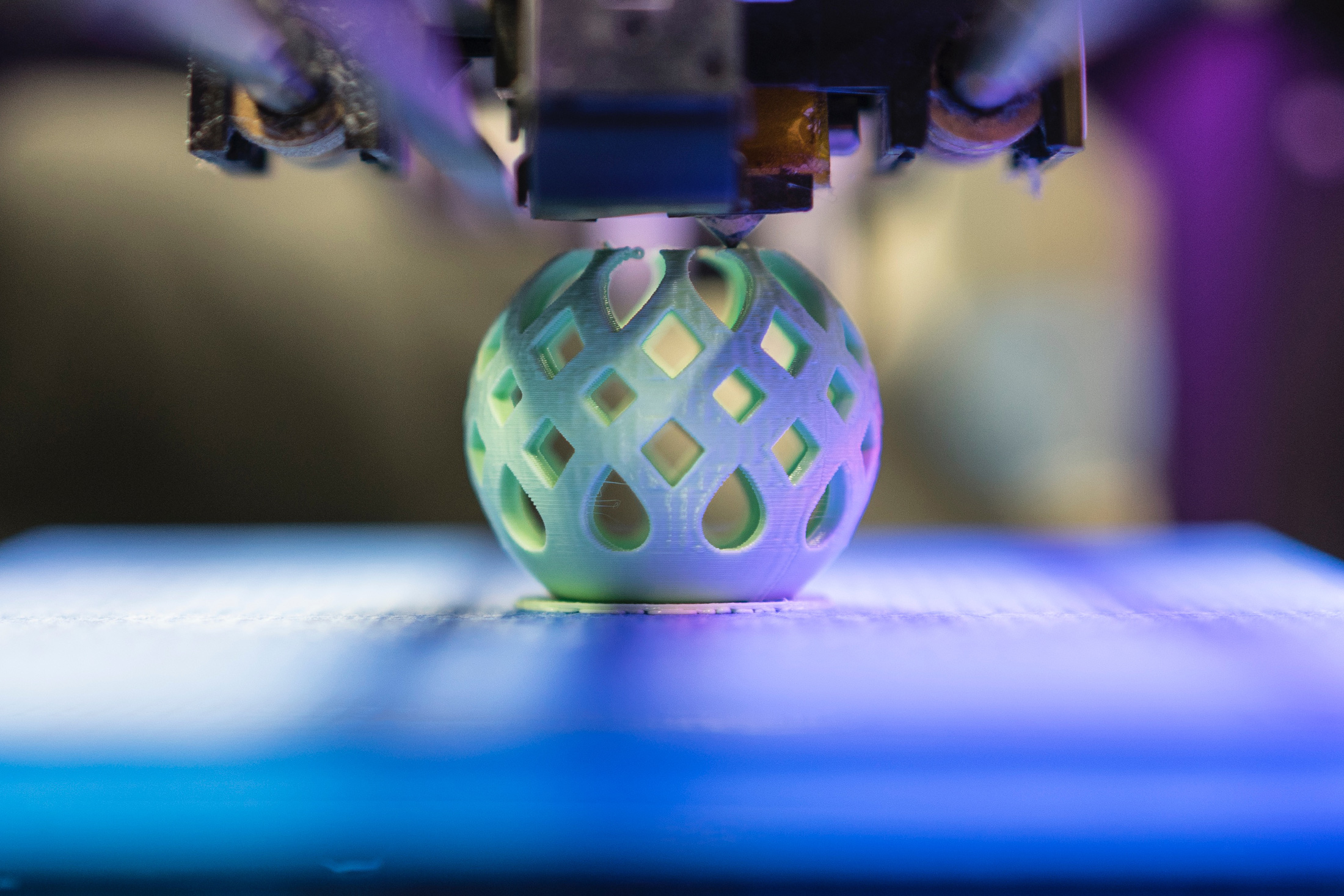
MultiJet printing (MJP)
The MJP uses an acrylic photopolymer, which offers a very high surface quality, precision and precision. The material is heated and applied layer by layer to the construction platform. There the material hardens immediately and is again post-cured with UV. The automatically generated support structures consist of a wax material with a lower melting temperature than the component material. The supports can thus be easily melted. The MJP technology is suitable for highly complex and sensitive applications.
Parts manufactured with then can be dyed and mechanically reprocessed. Special materials provide original models for the investment.
One advantage of Stereolithography is that a functional part can be built in a relatively short period of time. The amount of time required depends on the size, complexity and layer thickness the part will be built with. Parts can take anywhere from a few short hours to a day or more. Parts built with an SLA machine can be used as master patterns for RTV moulding, finished and painted or simply lightly sanded and may be used for shape studies or final presentation models.
This technology is used to create precise models. Printed items are created with high quality where the horizontal thickness is .032 mm. Elements are made on the printer with the professional series. Objects are printed while maintaining the finest details (accuracy of 0.025 – 0.05 mm) and have an extremely smooth surface by the use time of printing in the two materials at the same time – the photopolymer building material is cured using UV light and the wax supporting material. On the basis of prototypes created in the technology MJM creating silicone molds or casts for creating whole series of products, moving models(created during one print), functional prototypes. Models are durable and resistant to temperatures of up to approx. 80° C, they may be subject to further treatment.
- Prototypes for form, fit and functional testing
- SLA for prints that require high detail or for transparent object
- Moulds for lost-wax casting for jewellery applications
- Master models for high-precision industrial casting
- Producing final functional parts
- Entertainment (Figures and characters are brought to life in full color)
- 3D ceramic parts printing for medical and electronic applications
- Producing dental models and surgical guides
- Printing injection moulds for small series or functional tests